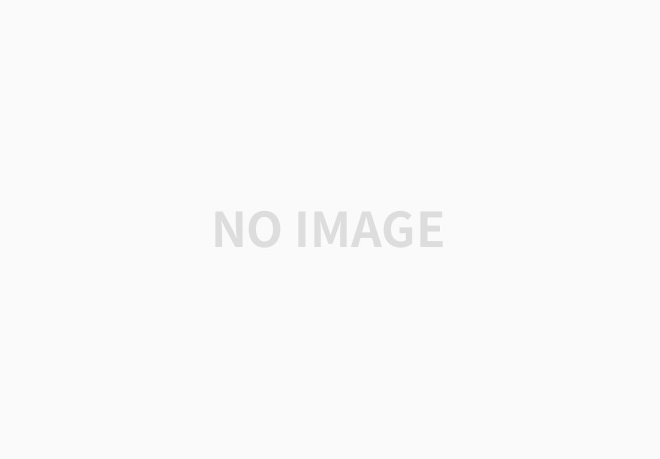
The main motive of the Lean 5S Problem Solving Framework is to arm every individual with methods and tools to handle obstacles and improve their productivity at work.
Whether you want to remove obstacles from the path to achieve your goals or raise your standards, Lean Manufacturing framework protocols would never let you down.
In a standardized lean management framework, anyone who is struggling with one or the other ongoing problem gets a solution that is driven by two major characteristics:
Everything mentioned in the problem should be based on verifiable facts and not on any type of assumption or analysis.
The problem-solving technique is a never-ending process. It begins when an improvement methodology is implemented. This implementation methodology is a guided opportunity for the individual to learn how to make progress.
Lean professionals firmly believe that the problem-solving process is disturbed when you end up making a common mistake or jump directly to a standard solution.
Professionals and business leaders do not fall under this trap because they know that typical business problems fall into four different categories; each need a different thought process followed by a specific improvement method and management choices.
Let’s look into the Four Types of Problems.
Type 1: Troubleshooting: Problem-solving technique that reactivates problem-solving skills that work instantly to make abnormal conditions known as usual. It may provide a quick solution but doesn’t eliminate the problem from the roots.
Type 2: Gap from Standard: This type of problem-solving is more structured problem-solving that defines the problem, sets a goal, analyzes the root cause, creates counter solutions, and follow-up after the process. The main goal is to remove the problem from the roots.
Type 3: Target Condition: It designs a new target state of improvement, so the problem-solving process is continuous. It may use old problem-solving methods, but they are used in a new and creative way to bring better results.
Type 4: Open-ended: This type of problem-solving is based on new and creative ways of recognizing opportunities to solve a problem. It creates unique rules that often look after new products, systems, processes, or values.
Lean thinkers help everyone to understand the problem and take the credit for seeing the problem and solving all types of issues by practicing:
- Inculcates a sense of responsibility in all worders, infusing a feeling of ownership.
- Prepares organizations to overcome obstacles at the root cause, so they do not end up seeing the bigger problem.
Developing a problem-solving culture in every organization gives an edge over competitors. Most competitors find it hard to match your level of problem-solving skills.
Lean Problem-Solving Process
You will go through a series of techniques when using the Lean 5S Problem solving techniques to get the desired results. Below-mentioned is the steps to problem-solving:
- Identifying the Problem – The first thing goes the first. Determining the actual problem is the key to get success.
- Go as precise as you can to find the actual problem. Look for minor details and other info.
- Break it Down – If the problem is more significant, break it down into more straightforward steps. This will help to find the solutions more clearly.
- Establish Targets – When you break the problem into simple steps, establish a target for the system you are working on. This will keep you on track on your way to problem-solving.
- Try to find the Root Cause – You can never solve any problem if you don’t know the root cause of it. Try to keep experimenting and find the root cause.
- Suggest some Counter solutions – Think out of the box and come up with some answers to find the root cause of the problem. You may need to take one or two actions to find the specific reason for the problem.
- Implementing Countermeasures – Implement the actions you thought in the previous step. You may try different activities on the test segment. This will help you find the root cause virtually. If you come up with something workable in a small system, expand your horizon and make sure you don’t make any mistakes.
- Test the Results – Check the results from different actions performed in the test area. If you can get fruitful results in a specific area, your problem-solving countermeasures may be successful. If not, don’t worry. Move back to the previous steps and find new actions to perform on the test area.
- Standardize – Once you find a solution, it’s time to standardize it on the entire problem.
- Come up with a new process and procedure: If you have managed to find a solution to a specific problem, coming up with a new approach and design is the last step in the problem-solving techniques.
Most professional teams use these problem-solving techniques either to solve a problem or improve their standards.